Thermal Extrusion Technology involves pushing a heated material through a die to create a continuous profile.
In the case of composite seamless pipes, this method ensures a uniform structure and eliminates the possibility of weak spots often found in welded pipes. The resultant pipe exhibits excellent mechanical properties, making it ideal for applications requiring high pressure and temperature resistance.
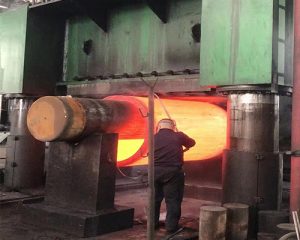
One of the most compelling advantages of this Thermal Extrusion Technology is its versatility.
It allows for the production of pipes with varying diameters and thicknesses, catering to a wide range of industries from oil and gas to chemical processing. Moreover, the use of composite materials further enhances the corrosion resistance and durability of these pipes, ensuring a longer service life.
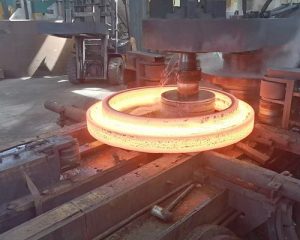
The production of seamless pipe by thermal extrusion technology requires that the pipe blank is hollow billet, the factory adopts:
- The hot extruded hollow tube blank is obtained by the method of drilling and then reaming by induction heating.
- After reaming, the temperature of the hollow tube blank decreases, and it is necessary to undergo induction heating to raise the temperature to the set preheating temperature of the blank.
- Before the extrusion begins, put the glass gasket that can play a lubricating role on the extrusion die, and lubricate the inner and outer surfaces of the hollow tube billet with glass powder. The preheated tube blank coated with glass powder lubrication is transported to the feeding table near the extrusion cylinder, and then rolled into the trough between the extrusion cylinder and the plunger, and the extrusion gasket is transported to the trough and close to the blank. After the extrusion rod moves slowly and is close to the extrusion pad, the extrusion mandrel is extended to connect the blank, the extrusion gasket and the extrusion mandrel into a whole.
- The extrusion rod moves forward under low extrusion pressure, and the billet is sent into the extrusion cylinder, and the groove automatically drops. With the increasing extrusion pressure, the extrusion rod moves forward gradually, and the pre-extrusion is carried out to fill the gap between the tube billet and the extrusion cylinder.
The production of bimetallic composite pipe by thermal extrusion technology, due to the extrusion pressure of high temperature and high pressure, produces a high section shrinkage rate, and produces a “forging and welding effect” on the bimetallic bonding surface, which promotes the rapid mutual diffusion and extensive combination between the two layers, which is what we usually say metallurgical bonding.
Therefore, this bimetallic tube can be used for high service temperatures. However, when bimetallic pipe is produced by hot extrusion, especially when the composite material is nickel-based alloy, the wall thickness of the composite pipe is prone to fluctuation and joint cracks are produced in the composite layer. The reason is that the deformation resistance of the base and the composite material is different, and the deformation resistance of the composite layer is large, while the deformation resistance of the base layer is small.
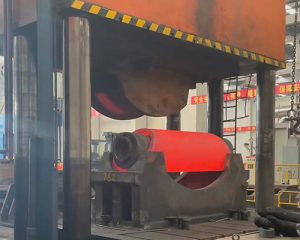
Our factory leads the way in this domain, leveraging cutting-edge machinery and skilled expertise to produce composite seamless pipes of unparalleled quality.
We pride ourselves on our stringent quality control measures, ensuring that each pipe meets the highest industry standards. Additionally, our commitment to innovation drives us to continually explore new materials and techniques, ensuring that our products stay at the forefront of technological advancement.
In conclusion, the thermal extrusion technology for manufacturing composite seamless pipes stands as a testament to human ingenuity and our relentless pursuit of improvement. As we look to the future, the continued evolution of this technology promises to reshape industries and pave the way for more efficient and sustainable practices. For those seeking reliable and high-performance piping solutions, composite seamless pipes produced through thermal extrusion offer an unmatched combination of strength, durability, and adaptability.