The integrity and reliability of composite metallurgy seamless steel pipes are paramount, especially when these are deployed in critical applications such as oil extraction, gas transportation, and structural engineering. Our company, a leader in advanced metallurgical solutions, is committed to ensuring that every pipe that leaves our facility not only meets but exceeds industry standards and client specifications through inspection of finished composite pipe.
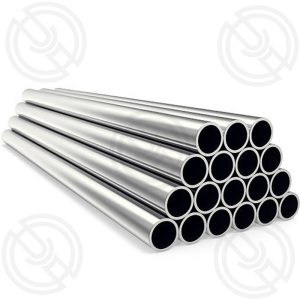
1.Inspection of finished composite pipe-Hydrostatic Pressure Test
A cornerstone of our quality assurance process is the hydrostatic pressure test, which simulates the actual working conditions that the pipes will endure. During this test, each pipe is filled with water and then pressurized to evaluate its ability to contain fluid under high pressure. This crucial test reveals the pipe’s strength and durability, ensuring they can handle the intended operating pressures without failure. Should even a microscopic flaw be present, it would be exposed by this rigorous examination.
(1) Strength test: first rise to 30% strength test pressure, stable pressure for 15min; Then rise to 60% strength test pressure, stable pressure for 15min; Check the tube during the voltage regulation, no abnormal phenomenon, rise to the strength test pressure. The test pressure is 1.5 times the design pressure.
(2)Tightness test: the test pressure is 1.0 times the design pressure, the pressure regulation time is 24h, the pipeline is not broken, no leakage is qualified. During the test, the pressure increase should be slow, and when it rises to 30% and 60% of the test pressure, the pressure increase should be suspended, and the line inspection should be carried.
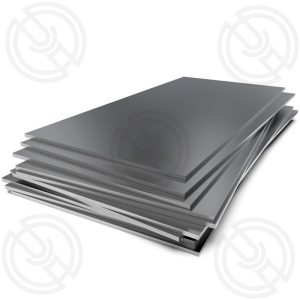
2.Inspection of finished composite pipe-Non-Destructive Testing (NDT)
Beyond the hydrostatic test, we employ a range of non-destructive testing methods to scrutinize the pipes thoroughly. These NDT techniques include ultrasonic testing, magnetic particle inspection, and eddy current testing. Ultrasonic testing uses high-frequency sound waves to detect internal defects such as cracks, voids, and inclusions. Meanwhile, magnetic particle inspection is particularly adept at revealing surface and sub-surface flaws by magnetizing the pipe and applying magnetic particles that align along any defect lines. Eddy current testing is employed to identify changes in the electrical properties of the material that could indicate defects such as cracks or corrosion.
According to customer requirements and products to decide which method of testing, the report issued after each method of testing can be called non-destructive testing report, that is, NDT test report.
Meet ASTM A265 CLASS1 Layered inspection requirements.
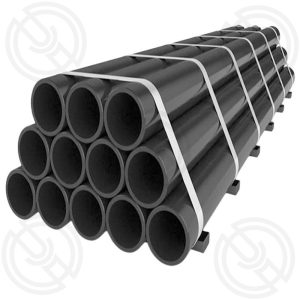
3.Inspection of finished composite pipe – dimensional tolerances
In addition to the stringent tests mentioned, we also measure each pipe against exacting dimensional tolerances. The diameter, wall thickness, and length are meticulously verified to ensure they conform to the project requirements. Our state-of-the-art measuring tools guarantee precision, allowing for a custom fit that aligns perfectly with our clients’ specifications. Whether it’s a standard dimension or a tailored size to suit unique operational needs, our facility is equipped to deliver accuracy down to the finest detail.
Take 219.1× (7.1+3) as an example:
Project | End requirements | Tube requirements |
Wall thickness | Multilayered3.26~3.76
grassroots-10~+12.5 |
|
Pipe diameter | ±0.75%D | |
Eccentricity | ≦0.75%D | |
Curvature | ≦0.15%L Maximum≦2mm/m | |
Length | 11.5m±0.5m |
Tailored to Your Needs: Customization at Its Finest
Our powerful production capabilities allow us to customize pipes according to individual customer requirements. From alloy selection to specific mechanical properties, we can fine-tune the manufacturing process to produce pipes that are tailor-made for each client’s particular application. This level of customization ensures that our pipes perform optimally in their intended environments, adding significant value to our clients’ operations.
Conclusion: Uncompromising Quality and Client Satisfaction
By integrating inspection of finished composite pipe: hydrostatic pressure tests, non-destructive evaluations, and strict dimensional controls into our manufacturing protocols, we provide an ironclad assurance of quality and performance. Our commitment to excellence has established us as a force to be reckoned with in the composite metallurgy sector. We take pride in our ability to meet and exceed expectations, consistently delivering seamless steel pipes that stand up to the rigors of industrial use while providing peace of mind to our customers. With our robust capabilities and unwavering dedication to quality, we are your trusted partner in seamless steel pipe technology.