ASTM A182 F53 is a high-performance duplex stainless steel designed for critical applications in the petrochemical, chemical, and marine industries. One of the key characteristics that set this material apart is its high PREN (Pitting Resistance Equivalent Number) value, which is a critical indicator of its resistance to pitting corrosion.
This article delves into the significance of the PREN value for ASTM A182 F53 flanges and how it impacts their performance in demanding environments.
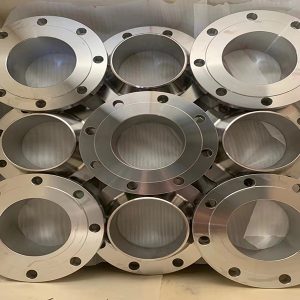
Introduction to ASTM A182 F53 Flanges
ASTM A182 F53 flanges are widely used in industries where resistance to corrosion is paramount. These flanges are made from a duplex stainless steel alloy that combines the properties of both ferritic and austenitic steels, offering a unique set of advantages. The alloy composition includes chromium, nickel, molybdenum, and nitrogen, which contribute to its high strength, toughness, and excellent corrosion resistance.
Understanding the PREN Value
The PREN value is a calculation used to estimate the relative resistance of stainless steels to pitting corrosion. The formula for PREN is typically given as:
PREN = %Cr + 3.3 * %Mo + 16 * %N
Where:
%Cr is the percentage of chromium in the alloy.
%Mo is the percentage of molybdenum in the alloy.
%N is the percentage of nitrogen in the alloy.
A higher PREN value indicates a greater resistance to pitting corrosion. For ASTM A182 F53, the PREN value typically exceeds 35, which is considered high and signifies a strong defense against pitting in chloride-containing environments.
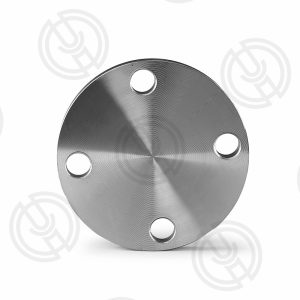
Significance of PREN for ASTM A182 F53 Flanges
The high PREN value of ASTM A182 F53 flanges is particularly significant in the following ways:
Corrosion Resistance: The high PREN value ensures that F53 flanges can withstand the aggressive corrosion environments commonly found in offshore platforms, chemical processing plants, and desalination facilities. The resistance to pitting is crucial for maintaining the integrity of the flange and preventing system failures.
Longevity: The enhanced corrosion resistance translates to a longer service life for F53 flanges. This reduces the need for frequent maintenance and replacement, which can be costly and disruptive to operations.
Safety: In industries where the risk of corrosion-related leaks can lead to catastrophic consequences, the use of F53 flanges with a high PREN value is essential for ensuring safety.
Applications of ASTM A182 F53 Flanges.
Due to their high PREN value, F53 flanges are preferred in a variety of applications, including:
Petrochemical Plants: F53 flanges are used in process lines, reactors, and storage tanks where exposure to corrosive chemicals is common.
Seawater Systems: In marine environments, F53 flanges are used in piping systems that come into contact with seawater, which is rich in chlorides.
Oil and Gas Exploration: Offshore platforms rely on F53 flanges for their resistance to the harsh conditions of the sea and the corrosive substances found in oil and gas extraction.
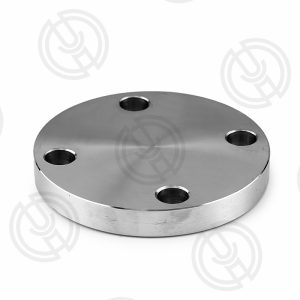
Conclusion
ASTM A182 F53 flanges with their high PREN value are a reliable choice for applications requiring exceptional resistance to pitting corrosion. The material’s ability to perform in challenging environments makes it an invaluable asset in the petrochemical, chemical, and marine industries.
However, it is important to note that while the PREN value provides a good indication of corrosion resistance, other factors such as crevice corrosion, stress corrosion cracking, and environmental conditions must also be considered when selecting materials for specific applications. With proper material selection and maintenance, ASTM A182 F53 flanges can ensure the safe and efficient operation of industrial processes.
With the development of industries such as petroleum, chemical, and marine engineering in our country, the application prospects of ASTM A182 F53 stainless steel will become even broader. However, in practical applications, it is necessary to select appropriate materials and corrosion protection measures based on specific working conditions to ensure the safety and stable operation of equipment.