Abstract
ASTM A182 F55 flanges are high-performance alloy steel flanges widely used in the petroleum, chemical, and marine engineering industries. These flanges are known for their excellent corrosion resistance, high strength, and durability. This article focuses on the tensile strength of ASTM A182 F55 flanges, discussing the factors affecting tensile strength, testing methods, and the significance of tensile strength in practical applications.
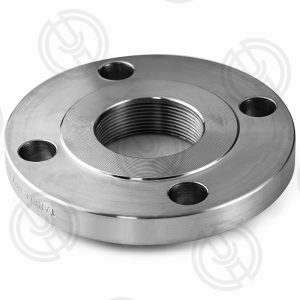
Introduction
Tensile strength is a crucial mechanical property of materials, indicating the maximum stress a material can withstand while being stretched or pulled before breaking. For ASTM A182 F55 flanges, high tensile strength is essential to ensure the integrity and reliability of pipeline systems under various working conditions. In this article, we will analyze the tensile strength of ASTM A182 F55 flanges and its importance in engineering applications.
Material Composition and Tensile Strength
ASTM A182 F55 flanges are made of alloy steel containing chromium, nickel, molybdenum, copper, and other alloying elements. These elements contribute to the material’s high tensile strength, as follows:
1.Chromium: Chromium forms chromium carbides, which help to refine the grain size and improve tensile strength.
2.Nickel: Nickel improves the toughness and ductility of the material, which indirectly affects tensile strength.
3.Molybdenum: Molybdenum enhances the strength and hardenability of the material, contributing to higher tensile strength.
4.Copper: Copper improves the material’s resistance to corrosion and also contributes to tensile strength.
Factors Affecting Tensile Strength
Several factors can influence the tensile strength of ASTM A182 F55 flanges:
1.Heat Treatment: The heat treatment process, including quenching and tempering, plays a significant role in determining the tensile strength of F55 flanges.
2.Microstructure: The grain size, phase composition, and distribution of alloying elements in the microstructure affect tensile strength.
3.Impurities: The presence of impurities, such as sulfur and phosphorus, can reduce the tensile strength of the material.
4.Surface Condition: Surface defects, such as cracks and pits, can act as stress concentrators, decreasing the tensile strength of the flange.
Testing Methods for Tensile Strength
The tensile strength of ASTM A182 F55 flanges is typically measured using universal testing machines. The following steps are involved in the tensile strength test:
1.Sample Preparation: A sample with a specific size and shape is cut from the F55 flange and polished to ensure a smooth surface.
2.Test Setup: The sample is securely mounted in the universal testing machine, with the clamps applying tension to the sample.
3.Test Execution: The machine gradually applies tension to the sample until it breaks, recording the maximum force applied and the corresponding elongation.
4.Data Analysis: Tensile strength is calculated by dividing the maximum force by the original cross-sectional area of the sample.
-300x300.jpg)
Test Results and Analysis
ASTM A182 F55 flanges have demonstrated high tensile strength in laboratory tests. The typical tensile strength of F55 flanges ranges from 690 to 895 MPa (100 to 130 ksi). The test results indicate the following:
1.High Tensile Strength: F55 flanges exhibit excellent tensile strength, making them suitable for applications subject to high mechanical stresses.
2.Ductility: The material shows good ductility, with elongation values typically ranging from 15% to 22%.
3.Uniformity: The tensile strength is consistent across different samples, indicating good quality control during manufacturing.
Significance of Tensile Strength in Practical Applications
High tensile strength is crucial for ASTM A182 F55 flanges in the following aspects:
1.Safety: Tensile strength ensures that the flanges can withstand the mechanical stresses encountered during operation, preventing failures and ensuring safety.
.Reliability: High tensile strength contributes to the reliability of pipeline systems, reducing the risk of leaks and other issues.
3.Design Optimization: Knowledge of the tensile strength of F55 flanges allows engineers to optimize the design of pipeline systems, reducing material usage and costs.
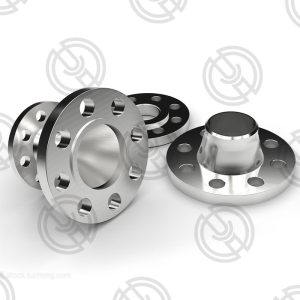
Conclusion
ASTM A182 F55 flanges exhibit high tensile strength, making them suitable for demanding applications in the petroleum, chemical, and marine engineering industries. Understanding the tensile strength of F55 flanges is essential for ensuring the safety, reliability, and optimal design of pipeline systems.
Through proper material selection, heat treatment, and quality control, the tensile strength of ASTM A182 F55 flanges can be effectively utilized in various engineering projects.