ASTM A182 F51 flanges have a wide range of applications in petroleum, chemical and offshore engineering, and their main advantage is excellent corrosion resistance.
In order to ensure the reliability of flanges in practical applications, the point corrosion test is very important. This paper introduces the application of ASTM A48A method in ASTM A182 F51 flange point corrosion test, and the guiding significance of test results for material selection and application.
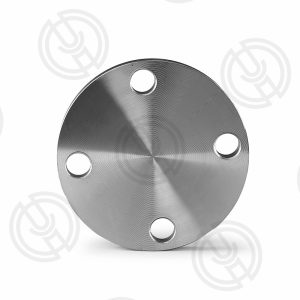
1. Introduction
Point corrosion is a form of local corrosion of stainless steel materials under specific environmental conditions, which seriously affects the performance and safety of equipment. The ASTM A182 F51 flange is a duplex stainless steel flange with good resistance to point corrosion. In order to evaluate its point corrosion resistance in practical applications, it is important to use G48A method for point corrosion test.
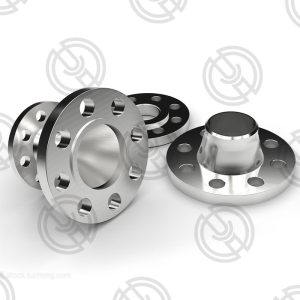
2. Introduction of G48A Method
The G48A method is a standard point corrosion test method developed by the American Society for Materials and Testing (ASTM), which is mainly used to evaluate the point corrosion sensitivity of stainless steel materials in chloride environments. By simulating the actual conditions, the corrosion soaking test was carried out to evaluate the point corrosion resistance of the material.
3. Test materials:
ASTM A182 F51 flange is selected as the test material in this test, and its main chemical composition is as follows:
1.Chromium: F51 stainless steel contains about 22% chromium. Chromium is a key element to improve the corrosion resistance of stainless steel, which can form a dense chromium oxide film on the surface of the material to protect the material from oxidation and corrosion.
2.Molybdenum: F51 also contains about 3% molybdenum. Molybdenum can significantly improve the resistance of stainless steel to pitting and crevice corrosion, especially in chloride environment.
3. Nickel (Nickel) : contains about 5% nickel, nickel can enhance the corrosion resistance and toughness of stainless steel.
4. Nitrogen: The addition of nitrogen helps to improve the corrosion resistance and strength of the material. In duplex stainless steel, nitrogen is an important alloying element that helps to improve the overall properties of the material.
Due to these chemical components of F51, it has good resistance to pitting, crevices and stress corrosion cracking, and is suitable for seawater, chemicals and pulp and paper industries. In the design and manufacturing process, it is also necessary to consider the welding process, heat treatment and machining characteristics of the material to ensure the quality and performance of the final product.
4. Test steps:
1. Sample preparation: Sample size 25mm×20mm×3mm is taken from ASTM A182 F51 flange to ensure smooth surface and no defects.
2. Test solution: Prepare 50% FeCl3 solution, pH value is 1.0±0.1.
3. Immersion test: Soak the sample in the test solution, the temperature is (35±1) ℃, soaking time is 24 hours.
4. Cleaning and observation: After the test, remove the sample, rinse it with clean water, and observe the point corrosion on the surface of the sample with a microscope.
5. Test results and analysis:
1. Test results: After 24 hours soaking test, slight pitting corrosion marks appeared on the surface of ASTM A182 F51 flange sample, but no obvious pitting pits were found.
2. Result analysis: The test results show that ASTM A182 F51 flanges have certain resistance to spot corrosion in chloride environment. In practical application, the material can be applied to moderate corrosion conditions.
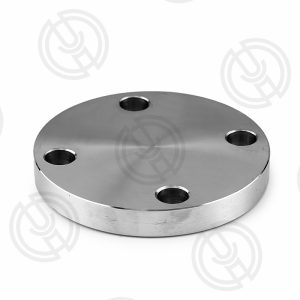
6. Conclusion
ASTM A182 F51 flanges were tested with G48A method to prove their good resistance to point corrosion in chloride environment.
In order to ensure the safety and reliability of flanges in practical applications, it is recommended to refer to the test results when selecting materials, and make reasonable selection according to the specific working conditions.
In addition, for severely corroded environments, appropriate anti-corrosion measures can be taken, such as coating protection, cathodic protection, etc., to reduce the risk of point corrosion.