Introduction:
ASTM A182 F51 flanges are widely used in industries such as oil, chemical, and pharmaceutical due to their excellent corrosion resistance and mechanical properties. One crucial aspect of these flanges is the ferrite content, which plays a significant role in determining their performance and suitability for various applications. This article aims to discuss the importance of ferrite content in ASTM A182 F51 flanges and its impact on their properties.
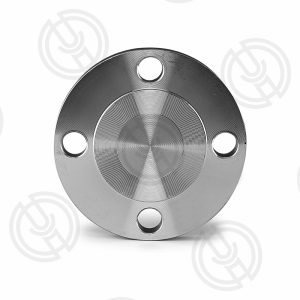
Understanding Ferrite Content:
Ferrite is a phase in the microstructure of steel that has a significant influence on the material’s mechanical and corrosion-resistant properties. In ASTM A182 F51 flanges, the ferrite content is carefully controlled to achieve the desired balance between strength, toughness, and resistance to corrosion.
The Role of Ferrite in Corrosion Resistance:
ASTM A182 F51 flanges are made from duplex stainless steel, which contains a mixture of austenite and ferrite phases. The ferrite content in these flanges contributes to their excellent corrosion resistance, particularly in environments where both oxidation and reduction reactions occur. The presence of ferrite helps to form a protective passive layer on the surface of the flange, which inhibits further corrosion.
Impact on Mechanical Properties:
The ferrite content in ASTM A182 F51 flanges affects their mechanical properties, including strength, toughness, and ductility. A higher ferrite content can increase the strength and hardness of the flange, making it more resistant to deformation and wear. However, excessive ferrite content can lead to reduced toughness and ductility, making the flange more susceptible to cracking and fracturing under certain conditions.
Controlling Ferrite Content:
To ensure the optimal ferrite content in ASTM A182 F51 flanges, manufacturers employ various heat treatment processes and alloying techniques. These processes help to achieve the desired ferrite-austenite balance, resulting in flanges with the required properties for specific applications.
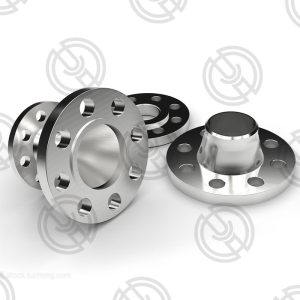
Testing Ferrite Content:
Manufacturers use several methods to measure and control ferrite content in ASTM A182 F51 flanges. Common techniques include magnetic particle inspection, ferrite meters, and microscopic analysis. These tests help ensure that the ferrite content falls within the specified range, guaranteeing the performance and reliability of the flanges.
The Importance of Ferrite Content in Different Applications:
The required ferrite content in ASTM A52 F51 flanges may vary depending on the application. For instance, in environments with high corrosion risks, a higher ferrite content may be necessary to enhance the flange’s resistance to degradation. Conversely, in applications where mechanical properties such as toughness and ductility are crucial, a lower ferrite content may be preferred.
Testing Methods for Ferrite Content To ensure that the ferrite content in ASTM A182 F51 flanges meets standards, the following are commonly used testing methods:
- Magnetic Particle Testing (MPT): By magnetizing the material and sprinkling magnetic particles on its surface, areas with higher ferrite content attract the particles, forming visible patterns, thus estimating ferrite content.
- Ferrite Meter: Using a portable electronic device that measures ferrite content based on the material’s magnetic permeability. The probe contacts the material surface and immediately displays the percentage of ferrite content.
- Microscopic Analysis: By preparing metallographic slices and observing them under a microscope, the area percentage of the ferrite phase can be calculated. This is an accurate but more costly destructive testing method.
- Hardness Testing: Although not a direct method for measuring ferrite content, hardness values can indirectly reflect ferrite content since the ferrite phase is typically softer than the austenite phase.
- X-ray Diffraction (XRD): By analyzing the X-ray diffraction patterns within the material, the proportion of ferrite and other phases can be determined accurately. This is a very precise laboratory technique.
- Magnetic Induction Method: Using an induction coil to measure the material’s magnetic permeability, thereby indirectly measuring ferrite content. Suitable for quality control during the production process.
-300x300.jpg)
Conclusion:
In conclusion, the ferrite content in ASTM A182 F51 flanges is a critical factor that influences their performance and suitability for various applications. By carefully controlling the ferrite content, manufacturers can ensure that these flanges possess the desired balance of corrosion resistance, strength, toughness, and ductility. As a leading provider of high-quality flanges and related products, our company is committed to maintaining the optimal ferrite content in our ASTM A182 F51 flanges, thereby delivering reliable and durable solutions to our clients in the oil, chemical, and pharmaceutical industries.