Abstract:
ASTM A182 F55 flanges, widely used in industries such as petroleum, chemical, and pharmaceutical, are corrosion-resistant materials whose quality is directly related to the safe operation of equipment. This paper analyzes the harmful metal phases in ASTM A182 F55 flanges, discussing their causes and effects on flange performance, providing a theoretical basis for improving flange quality.
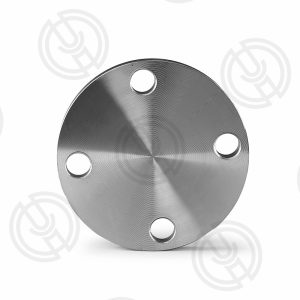
Introduction:
ASTM A182 F55 flanges are a type of duplex stainless steel flange known for their good corrosion resistance, mechanical properties, and weldability. However, during the production process, factors such as raw materials and production techniques can lead to the presence of harmful metal phases in the flanges, which can adversely affect their performance. This paper aims to study the types, causes, and effects on flange performance of harmful metal phases in ASTM A182 F55 flanges.
Types and Causes of Harmful Metal Phases:
1.Ferrite (δ phase):
Ferrite is one of the main phases in duplex stainless steel, and an appropriate amount of ferrite can improve the material’s mechanical properties and corrosion resistance. However, an excessive amount of ferrite can lead to a decrease in the plasticity and toughness of the flange, thus affecting its performance.
Cause: The excessive ferrite content is mainly due to raw material composition segregation and improper heat treatment processes.
2.Intergranular Corrosion Phase (χ phase):
The intergranular corrosion phase is a harmful phase that precipitates at the grain boundaries and can lead to a decrease in the flange’s corrosion resistance. The formation of the χ phase is related to the segregation of alloying elements such as chromium and molybdenum.
Cause: High heat treatment temperatures, prolonged holding times, and other factors can lead to the precipitation of the χ phase.
3.Sigma Phase (σ phase):
The sigma phase is a brittle phase that can severely affect the plasticity and toughness of the flange. The formation of the sigma phase is related to the segregation of alloying elements such as nickel and molybdenum.
Cause: Improper heat treatment processes and slow cooling rates can lead to the precipitation of the sigma phase.
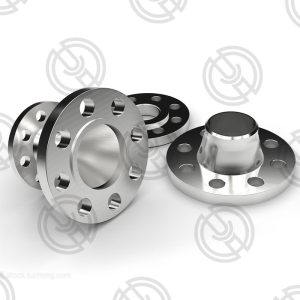
Impact of Harmful Metal Phases on ASTM A182 F55 Flange Performance:
1.Mechanical Properties:
The presence of harmful metal phases can lead to a decrease in the mechanical properties of ASTM A182 F55 flanges. Excessive ferrite content reduces the plasticity and toughness of the flange; the precipitation of intergranular corrosion and sigma phases can decrease the strength and toughness of the flange.
2.Corrosion Resistance:
Harmful metal phases can reduce the corrosion resistance of ASTM A182 F55 flanges. Excessive ferrite content weakens the flange’s resistance to uniform corrosion in corrosive environments; the precipitation of intergranular corrosion phases can lead to intergranular corrosion in specific corrosive media; the presence of sigma phases can accelerate the corrosion rate of the flange in corrosive environments.
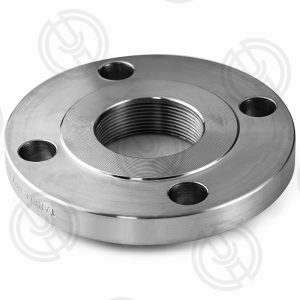
Conclusion:
This paper has analyzed the harmful metal phases in ASTM A182 F55 flanges, discussing the causes and effects on flange performance of ferrite, intergranular corrosion phases, and sigma phases. To improve the quality of ASTM A182 F55 flanges, it is necessary to strictly control the composition of raw materials and optimize heat treatment processes to reduce the precipitation of harmful metal phases. This will help enhance the mechanical properties and corrosion resistance of the flanges, ensuring the safe operation of equipment.
Hebei Yanshan Enfei Pipeline Technology Co., Ltd., established in 2019, specializes in the production of special material forgings such as ASTM A182 F55 flanges. The company is certified by the Norwegian national petroleum standard NORSOK M-650, demonstrating the high quality and reliability of its products in the offshore and natural gas industries.
Enfei Pipeline Technology’s product range includes a variety of corrosion-resistant and high-performance pipeline components, meeting the demanding needs of industrial applications in severe environments.