ASTM A182 F60 flange are widely used in various industries for their excellent mechanical properties and corrosion resistance. To ensure the reliability and safety of these flanges, it is crucial to conduct pitting corrosion tests. This article discusses the G48 A method for performing pitting corrosion tests on ASTM A182 F60 flanges.
-300x300.jpg)
-
Understanding ASTM A182 F60 Flanges:
ASTM A182 F60 flanges are forged steel flanges designed for use in high-temperature and pressure applications. These flanges are made from an alloy containing chromium, nickel, and molybdenum, which provides excellent resistance to corrosion and high-temperature oxidation. The F60 grade is specifically chosen for its resistance to pitting corrosion in aggressive environments.
-
Importance of Pitting Corrosion Test:
Pitting corrosion is a localized form of corrosion that can lead to the formation of small holes or cavities on the metal surface. In industries such as oil and gas, chemical processing, and pharmaceuticals, pitting corrosion can cause significant damage to equipment and compromise safety. Conducting pitting corrosion tests on ASTM A182 F60 flanges helps identify their resistance to this type of corrosion, ensuring their suitability for specific applications.
Point corrosion, also known as small hole corrosion, is a kind of corrosion concentrated in a small range of metal surface and deep into the metal interior or even perforation. Metals with self-passivation characteristics, such as stainless steel, aluminum and aluminum alloys, often suffer pitting corrosion in media containing chloride ions. Carbon steel can also be pitted in many chlorine-containing media.
The main characteristics of pitting corrosion are the following three aspects:
(1) pitting occurs mostly on the metal with passivation film on the surface or on the metal with negative polar coating on the surface (such as tin, copper, nickel on the surface of carbon steel). When the damage occurs at some points on these films, the metal matrix under the damage area forms an activation – passivation corrosion battery with the undamaged area of the film. The passivation surface is the cathode and the area is much larger than the activation area, and the corrosion develops into a small hole deep.
(2) pitting occurs in media containing special ions, such as stainless steel is particularly sensitive to halogen ions, and the order of action is Cl- > Br- > I-.
(3) Pitting usually occurs above a critical potential, the potential is called pitting potential or breaking potential, and stops below a certain potential, and this potential is called protection potential or re-passivation potential.
When the potential is greater than the pitting potential, the pitting corrosion occurs and develops rapidly. When the potential is between pitting potential and protection potential, the pitting corrosion that has occurred continues to develop, but no new pitting hole is produced. When the potential is below the protection potential, pitting does not occur, that is, no new pitting will occur, and the existing pitting holes will be passivated and no longer develop.
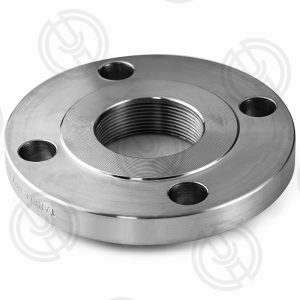
-
G48 A Method for Pitting Corrosion Test:
The G48 A method is a standardized test procedure developed by ASTM International for evaluating the pitting corrosion resistance of stainless steels and nickel-based alloys. The test involves subjecting the sample to a controlled corrosive environment and measuring the number and depth of pits formed.
3.1. Test Setup:
The G48 A test is performed using a glass cell containing a 6% ferric chloride solution at a temperature of 50°C ± 3°C. The cell is equipped with a reference electrode, a counter electrode, and a specimen holder. The ASTM A182 F60 flange sample is mounted in the specimen holder and immersed in the test solution.
3.2. Test Procedure:
The test is conducted for a duration of 24 hours. During this period, a constant potential of 1.1 times the critical pitting potential (Ecp) of the material is applied to the sample. The critical pitting potential is determined through preliminary tests and is specific to the material being tested.
3.3. Evaluation:
After the test, the sample is removed from the test solution, rinsed, and dried. The number and depth of pits formed on the sample surface are measured using a microscope. The results are compared to the acceptable limits specified by ASTM A182 F60 standards.
-
Interpretation of Results:
If the number and depth of pits formed on the ASTM A182 F60 flange sample are within the acceptable limits, the material is considered to have adequate resistance to pitting corrosion. However, if the pits exceed the specified limits, the material may require additional treatment or coating to improve its corrosion resistance.
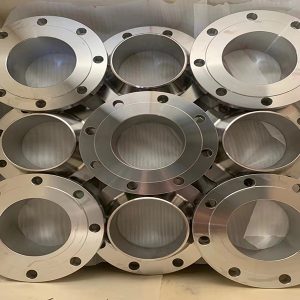
Conclusion:
Conducting pitting corrosion tests on ASTM A182 F60 flanges using the G48 A method is essential to ensure their resistance to pitting corrosion in aggressive environments. By following this standardized test procedure, manufacturers and end-users can confidently select and use ASTM A182 F60 flanges for various applications, ensuring reliability and safety.