ASTM A234 WP11 Pipe Fittings – Complete Technical Guide
1. Material Specification Overview
ASTM A234 WP11 is a chromium-molybdenum alloy steel fitting specification for high-temperature and high-pressure service. These fittings are commonly used in:
– Power generation plants
– Petrochemical refineries
– Oil and gas pipelines
– High-temperature processing systems
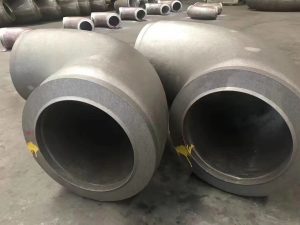
2. Material Grades and Classes
| Grade | Class | Key Characteristics |
|——-|——-|———————|
| WP11 | Class 1 | Standard chromium-molybdenum alloy |
| WP11 | Class 2 | Modified composition for improved weldability |
| WP11 | Class 3 | Enhanced strength properties |
3. Chemical Composition Requirements (%)
| Element | Class 1 | Class 2 | Class 3 |
|———|———|———|———|
| Carbon (C) | 0.05-0.15 | 0.05-0.20 | 0.05-0.20 |
| Manganese (Mn) | 0.30-0.60 | 0.30-0.80 | 0.40-0.70 |
| Phosphorus (P) | ≤0.03 | ≤0.04 | ≤0.03 |
| Sulfur (S) | ≤0.03 | ≤0.04 | ≤0.03 |
| Silicon (Si) | 0.50-1.00 | 0.50-1.00 | 0.50-1.00 |
| Chromium (Cr) | 1.00-1.50 | 1.00-1.50 | 1.00-1.50 |
| Molybdenum (Mo) | 0.44-0.65 | 0.44-0.65 | 0.44-0.65 |
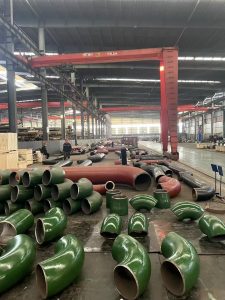
4. Mechanical Properties
| Property | Class 1 | Class 2 | Class 3 |
|———-|———|———|———|
| Tensile Strength (MPa) | 415-585 | 485-655 | 520-690 |
| Yield Strength (MPa) | 205 min | 275 min | 310 min |
| Elongation (%) | 20 min | 20 min | 20 min |
| Hardness (HB) | ≤197 | ≤197 | ≤197 |
5. Temperature Range and Pressure Ratings
– Service Temperature: -20°F to 1000°F (-29°C to 538°C)
– Maximum Allowable Stress:
– 14.4 ksi @ 100°F (99 MPa @ 38°C)
– 7.5 ksi @ 1000°F (52 MPa @ 538°C)
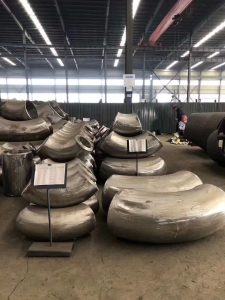
6. Manufacturing Standards
– **Fabrication Standard**: ASTM A234
– **Dimensional Standards**:
– ASME B16.9 (Butt-welding fittings)
– ASME B16.28 (Wrought steel butt-welding short radius elbows)
– **Testing Requirements**: Hydrostatic, NDT, mechanical testing
7. Available Fitting Types
1. **Elbows** (45°, 90°, 180°)
2. **Tees** (straight and reducing)
3. **Reducers** (concentric and eccentric)
4. **Caps**
5. **Stub Ends**
6. **Crosses**
7. **Lap Joint Stub Ends**
8. Heat Treatment Requirements
– **Normalizing**: 1600-1700°F (870-925°C)
– **Tempering**: 1200-1350°F (650-730°C)
– **Post-Weld Heat Treatment (PWHT)**: Required for all welded fittings
9. Quality Control and Testing
– **Mandatory Tests**:
– Hydrostatic testing
– Tensile testing
– Hardness testing
– **Optional Tests**:
– Charpy V-notch impact testing
– Positive Material Identification (PMI)
– Radiographic examination
10. Comparison with Similar Grades
| Grade | Cr Content | Mo Content | Key Difference |
|——-|———–|———–|—————-|
| WP5 | 4-6% | 0.44-0.65% | Higher chromium |
| WP9 | 8-10% | 0.90-1.10% | Higher alloy content |
| WP22 | 1.90-2.60% | 0.87-1.13% | Different Cr-Mo ratio |
11. Welding Considerations
– **Preheat Temperature**: 300-400°F (150-200°C)
– **Interpass Temperature**: ≤600°F (315°C)
– **Recommended Electrodes**:
– E8018-B2 (SFA 5.5)
– ER80S-B2 (SFA 5.28)
– **PWHT Requirements**: Mandatory after welding
12. Corrosion Resistance
– **Oxidation Resistance**: Good up to 1000°F (538°C)
– **Sulfide Stress Cracking**: Requires proper heat treatment
– **General Corrosion**: Better than carbon steel but inferior to stainless
13. Applications in Industry
1. **Power Generation**:
– Boiler feedwater systems
– Steam piping
– High-pressure turbine lines
2. **Petrochemical**:
– Catalytic cracking units
– Hydroprocessing systems
– Reformer units
3. **Oil and Gas**:
– Transmission pipelines
– Refinery process piping
– Heat exchanger systems
14. Purchasing Specifications
When ordering ASTM A234 WP11 fittings, specify:
– Material grade and class
– Type and size of fitting
– Schedule or wall thickness
– End preparation (beveled, plain)
– Heat treatment requirements
– Testing and certification needs
– Surface finish requirements
15. Maintenance and Inspection
– **Regular Inspection**:
– Visual examination for cracks or deformation
– Ultrasonic thickness measurements
– Hardness testing in HAZ areas
– **Replacement Criteria**:
– Wall thinning >10% of original thickness
– Visible cracks or defects
– Excessive creep deformation
This comprehensive specification ensures proper selection and application of ASTM A234 WP11 pipe fittings for critical high-temperature services. The chromium-molybdenum alloy composition provides enhanced strength and creep resistance compared to standard carbon steel fittings, making them suitable for demanding industrial applications.