In the realm of industrial piping systems, composite pipes are favored for their enhanced durability and resistance to corrosion. However, ensuring these attributes composite pipe finished product inspection is required that evaluate various properties including bonding strength, chemical composition, mechanical performance, hardness, metallurgical structure, and susceptibility to hydrogen-induced cracking (HIC).
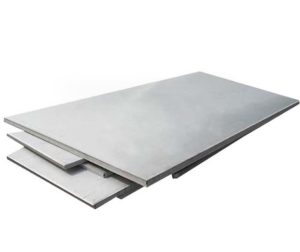
1.Composite pipe finished product inspection:Bond strength test
inspection standard:ASTM A265
acceptance standard shear strength:328Mpa≧250Mpa
Bonding Strength Testing is paramount as it ensures the integrity of the interface between the base layer and the cladding material. This test often involves applying force or pressure to measure the resistance to delamination, which can be critical in high-pressure applications.
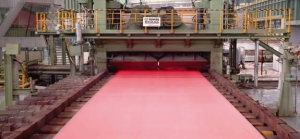
2.Composite pipe finished product inspection:Layered chemical composition
Mark | chemical component % | |||||
C | Si | Mn | P | S | Cr | |
≦0.030 | ≦0.50 | ≦1.00 | ≦0.03 | ≦0.02 | 19.5-23.5 | |
N08825 | 0.016 | 0.13 | 0.3 | 0.02 | 0.001 | 23.23 |
Mark | chemical component % | |||||
Ni | Mo | Cu | Ti | Al | Fe | |
38.0-46.0 | 2.5-3.5 | 1.5-3.0 | 0.6-1.20 | ≦0.20 | margin | |
N08825 | 40.44 | 3.19 | 2.18 | 0.67 | 0.1 | |
Remarks | Other requirements shall be implemented in accordance with API5L, and finally according to the billet agreement |
PREN=[1%Cr+3.3%Mo+16%N]=33.48≥31
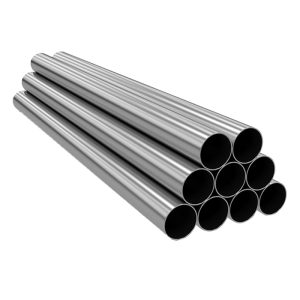
Chemical Composition Analysis of the Cladding Layer is essential because it directly influences corrosion resistance and compatibility with transported fluids. Techniques such as spectroscopy are employed to determine the exact elemental constituents, ensuring they meet specified standards.
-
Composite pipe finished product inspection:Mechanical properties of base
texture | Tensile Rm | Yield Rt0.5 | yield strength ratio Rt0.5/Rm | Hardness HV10 |
L360QS | ≥460-630 | ≥360-485 | ≤0.90 | ≤220 |
588 | 499 | 0.85 | 186 |
Mechanical Performance Evaluation of the Base Layer is vital for understanding its ability to withstand stresses and strains during operation. Tensile strength, yield strength, and elongation tests provide a clear picture of the pipe’s overall structural integrity under load.
-
Composite pipe finished product inspection:Laminated hardness
Laminated hardness is 179HV10, (Average not more than 315HV10,A single value cannot exceed 345HV10)
Hardness Testing of the Cladding Layer serves as an indicator of its resistance to wear and deformation. The hardness value can also indirectly suggest other properties like tensile strength and fatigue limit.
-
Composite pipe finished product inspection:Base and layer metallographic structure
Base grain size:level 10 (inspection standard ASTM E112 No less than level 8)
metallographic structure: Base – tempered sorbite
Laminated – austenite
Metallographic Examination of both Base and Cladding Layers involves microstructural analysis to assess grain size, phase distribution, and the presence of imperfections such as inclusions or voids. This evaluation provides insights into material processing quality and predicts potential failure modes.
6.Composite pipe finished product inspection:Base HIC
test standard | NACE TM0284-2003 | specimen size | 100mm×20mm ×thickness(non-parity) |
test condition | test solution Standard NACE A solution | ||
H2S partial pressure | 0.1Mpa | ||
Degreasing method | Trichloroethane degreasing | ||
PH before the test | 2.7 | ||
PH after the test | 3.9 | ||
test temperature | 25℃ | ||
test cycle | 96 hours | ||
acceptance standard | CLR≤5% CTR≤1.5% CSR≤0.5% Number of hydrogen bubbles per sample≤5 Hydrogen bubbling area ratio≤1% Hydrogen bubble diameter≤1mm |
Lastly, Hydrogen-Induced Cracking (HIC) Assessment is specifically crucial for the base layer. Exposure to hydrogenous environments can lead to cracking in susceptible materials, hence HIC testing evaluates the material’s resilience in such conditions, ensuring operational safety and longevity.
Through these composite pipe finished product inspection, a thorough evaluation of the composite pipe’s performance can be achieved, ensuring stability and reliability under high pressure and corrosive environments. Regular and appropriate inspection helps prevent future structural failures, reduce maintenance costs, and ensure the safety and long-term operation of pipeline systems.