In the world of piping and mechanical engineering, flanges play a crucial role in connecting pipes, valves, and other components.
The Flange Face of a flange is an essential characteristic that affects the sealing capability and suitability for different applications.
This article delves into the various types of flange faces, their unique features, suitable scenarios for use, and their common English abbreviations.
Keywords: Flange Face Types
The surface of the flange that makes contact with the gasket is called the “face.” The face is one of the most crucial parts of the flange as it seals against the gasket to prevent leaks. Flange faces can be raised face, flat face, tongue and groove (T&G), ring type, or male and female type, depending on the application and the required level of preload to ensure a tight seal.
In addition to their role in creating a secure connection, flanges also play a vital role in the maintenance and assembly of piping systems. They provide easy disassembly for maintenance, inspection, or replacement of system components without needing to disrupt the entire pipeline. Flanges come in various materials such as carbon steel, stainless steel, and aluminum, each suited to different service conditions like pressure, temperature, and chemical compatibility. Sizes, pressure classes, and dimensions of flanges are standardized according to international standards such as ANSI (American National Standards Institute), ASME (American Society of Mechanical Engineers), and EN (European Norm), ensuring interchangeability and consistency in industrial applications worldwide.
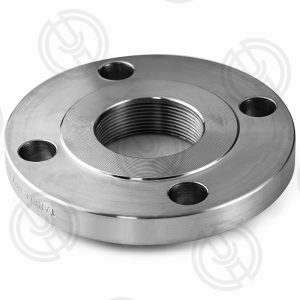
1.Flat Face (FF) Flanges:
Flat face flanges are characterized by a smooth, non-protruding surface.
They are typically used with a gasket that fills the gap between the two mating surfaces to create a seal. Flat face flanges are economical and widely used in low-pressure applications where there is no risk of the gasket being blown out. However, they may not be suitable for high temperatures or pressures due to potential leakage issues.
2.Raised Face (RF) Flanges:
Raised Flange Face Types feature a protrusion in the center of the flange that helps to distribute the clamping force over the gasket more evenly. This design enhances the sealing ability compared to flat face flanges. Raised face flanges are often used in services requiring a reliable seal under moderate pressure and temperature conditions. They are versatile and can be found in many industrial processes.
3.Tongue and Groove (TG) Flanges:
Tongue and groove flanges have a tongue on one flange that fits into a corresponding groove on the other, providing additional protection against twisting and misalignment.
Flange Face Types offers a positive lock for the gasket, making it ideal for high-pressure and high-temperature applications. The tongue and groove design ensures that the gasket remains in place and does not extrude under extreme conditions.
4.Ring Joint (RJ) Flanges:
Ring joint flanges are specially designed for severe service conditions, featuring a recessed groove that houses a metal ring to provide the seal. Flange Face Types is compressed between the two flanges when bolted together, creating a highly effective seal. Ring joint flanges are commonly used in critical applications such as steam lines, large diameter piping, and high-pressure situations where exceptional performance is required.
5.Male and Female Face (MF) Flanges:
Male and female face flanges consist of a male face that has a raised face and fits into a corresponding female face with a matching recess. This configuration provides a good seal and prevents the gasket from being blown out. Male and female face flanges are suitable for medium to high-pressure services and can offer better alignment than flat Flange Face Types.
6.Conclusion:
Understanding the different flange face is essential for ensuring proper sealing and selecting the appropriate flange for specific applications. From flat face flanges for simple, low-pressure uses to ring joint flanges for demanding high-pressure environments, each type has its unique advantages and limitations. By choosing the right flange face type, engineers can optimize system performance and ensure reliable operation in diverse piping systems.