Heat treatment is an integral part of the metallurgical process, serving to alter the physical and sometimes chemical properties of a material. This is achieved by controlling the heating and cooling of the material to achieve desired changes in its microstructure. The objectives of heat treatment can range from improving hardness to increasing toughness or ductility, enhancing wear resistance, reducing brittleness, or even changing the magnetic properties of the metal.
- Introduction to Heat Treatment
Heat treatment is a broad term that encompasses several processes used to manipulate the properties of a metal through thermal processing. It’s a crucial step in manufacturing as it can significantly enhance the performance of metal parts. The science behind heat treatment lies in understanding how different temperatures and cooling rates affect the crystalline structure of metals, which in turn affects their mechanical properties.
- Basic Terms and Concepts
Before delving into the specifics of heat treatment processes, it’s essential to understand some basic terms and concepts:
Microstructure: The microscopic structure of a material, including its phases, grain size, and shape.
Phase transformation: A change in the crystal structure of a material due to temperature variations or chemical reactions.
Eutectoid steel: A type of steel containing the correct proportion of carbon (about 0.8%) to form pearlite at eutectoid temperature.
Austenite: A solid solution of carbon in gamma-iron, which forms at high temperatures.
Martensite: A hard, acicular form of iron that contains carbon in solid solution, formed by quenching austenite.

- Heat Treatment Processes
There are several types of heat treatment processes, each with its own purpose and technique. Here are the most common ones:
Annealing: Involves heating the metal to a certain temperature, holding it for a period, and then allowing it to cool slowly in the furnace. This process is used to soften metals, improve machinability, reduce hardness, and refine the grain size.
Normalizing: Similar to annealing but with faster cooling, usually in air. It is used to refine grain size and improve mechanical properties while maintaining strength.
Quenching: Rapid cooling, usually in water or oil, to obtain a martensitic structure. Quenching can dramatically increase hardness and strength but may introduce internal stresses.
Tempering: Heating the previously hardened steel to a lower temperature than quenching, followed by slow cooling. This reduces brittleness and relieves internal stresses induced by quenching.
Case Hardening: Used to increase the surface hardness without affecting the core properties. Carbon is added to the surface, creating a harder outer layer when quenched.
Carburizing: Introducing carbon into the surface of a metal, typically steel, to increase its hardness after quenching and tempering.
Nitriding: Introducing nitrogen into the surface of a metal to form a hard compound layer, improving wear resistance and fatigue strength.
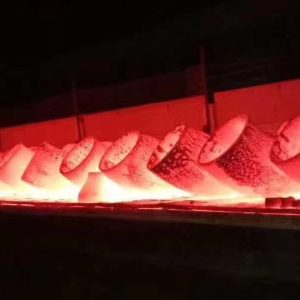
- Importance of Controlled Cooling Rates
The rate at which a metal cools plays a crucial role in determining its final properties. Slow cooling allows time for diffusion to occur, leading to a more uniform distribution of alloying elements. Rapid cooling can ‘freeze’ the microstructure, trapping in desirable properties such as hardness but also potentially causing residual stresses.
- Effects on Material Properties
The effects of heat treatment on material properties are multifaceted:
Hardness and Strength: Typically increased through processes like quenching and tempering.
Toughness: Can be improved by normalizing or through controlled quenching and tempering cycles.
Ductility and Malleability: Annealing can make metals softer and easier to work with.
Fatigue Resistance: Nitriding and carburizing can enhance a metal’s ability to resist fatigue failure.
Wear Resistance**: Case hardening and nitriding can create a harder surface that resists wear better.
Corrosion Resistance: While not typically the main goal, certain heat treatments can influence corrosion behavior.
- Applications of Heat Treatment
Heat treatment has numerous applications across various industries:
Automotive: Gears, shafts, and crankshafts often undergo heat treatment for improved performance and durability.
Aerospace: Aircraft components are heat treated to ensure they can withstand high stresses and temperatures.
Manufacturing: Machine parts and tools are routinely heat treated to extend their service life and maintain cutting edges.
Construction: Reinforcing bars (rebars) are often heat treated for better bonding with concrete.
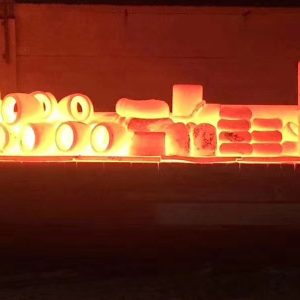
- Conclusion
The field of heat treatment is complex and nuanced, requiring careful control over temperature, time, and cooling rates. By manipulating these variables, engineers can tailor the properties of metals to suit specific applications, enhancing their functionality and longevity. As materials science continues to advance, so too do the techniques and technologies involved in heat treatment, ensuring that this critical aspect of manufacturing remains at the forefront of industrial progress.