Metallurgical composite pipes are a crucial component in various industries, including oil and gas, chemical, and nuclear sectors. The reliability and safety of these pipes are paramount, making the inspection process a critical step in ensuring their integrity.
Our company excels in this domain by focusing on three primary types of corrosion that can compromise the structural integrity of composite pipes: Stress Corrosion Cracking (SCC), Intergranular Corrosion, and Pitting Corrosion. This article highlights our specialization and advantages in detecting and managing these corrosion types during the final inspection of metallurgical composite pipes.
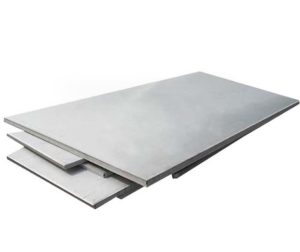
-
Metallurgical Composite Pipe Inspection-multiple layer
Hydrogen sulfide partial pressure:6Mpa
Partial pressure of sulfur dioxide:4Mpa, PH3.5,temperature:90℃,Four-point bending test under 80%AYS,No SCC crack was found on the tensile surface.
K++Na + mg/L | Ca2+ mg/L | Mg2+ mg/L | Cl– mg/L | SO4 2- mg/L | HCO3 – mg/L | CO3 2-mg/L | OH –mg/L | total salinity | water type |
1117 | 4190 | 1345 | 12838 | 66 | 294 | 0 | Cacl2 |
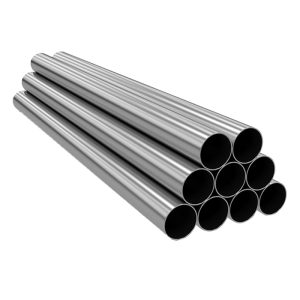
Stress Corrosion Cracking (SCC) is a brittle fracture that occurs in certain metals under the combined influence of tensile stress and a specific corrosive environment. Recognizing the potential for SCC, we employ advanced non-destructive testing (NDT) techniques such as ultrasonic testing and X-ray diffraction to detect micro-cracks before they become critical. Our specialized equipment allows for precise monitoring of the pipe’s stress levels and the detection of anomalies that may lead to SCC. Furthermore, our team of experts is well-versed in metallurgical composite pipe inspection, ensuring that any indications of SCC are accurately identified and addressed.
Stress Corrosion Cracking (SCC) is a brittle fracture that occurs in certain metals under the combined influence of tensile stress and a specific corrosive environment. Recognizing the potential for SCC, we employ advanced non-destructive testing (NDT) techniques such as ultrasonic testing and X-ray diffraction to detect micro-cracks before they become critical. Our specialized equipment allows for precise monitoring of the pipe’s stress levels and the detection of anomalies that may lead to SCC. Furthermore, our team of experts is well-versed in metallurgical composite pipe inspection, ensuring that any indications of SCC are accurately identified and addressed.
2.Metallurgical Composite Pipe Inspection-Multilayer intergranular corrosion
ASTM A262, No cracks were found in method E
ASTM A262, method C 5×48h,average corrosion rate:0.05m/mouth(0.06)
ASTM G28A A comparative test of sensitization and unsensitization:1.11(2.0)
Intergranular Corrosion occurs along the grain boundaries of metal, often resulting from impurities or alloying elements segregating at these boundaries. To combat intergranular corrosion, our inspection protocol includes rigorous material composition analysis and microstructural evaluation using techniques such as scanning electron microscopy (SEM) and energy-dispersive X-ray spectroscopy (EDS). These methods allow us to assess the distribution of elements within the pipe’s material, identifying areas susceptible to intergranular attack. Additionally, we perform corrosion testing under simulated service conditions to evaluate the resistance of the material to intergranular corrosion, providing assurance of the pipe’s long-term performance.

3.Metallurgical Composite Pipe Inspection-Multilayer point corrosion
ASTM G48 Method A corrosion rate:3.2g/m2
Pitting Corrosion is localized corrosion that leads to the formation of small cavities on the surface of metals. It can significantly reduce the mechanical strength of a pipe and is challenging to detect in its early stages. Our company leverages electrochemical impedance spectroscopy (EIS) and high-resolution imaging techniques like digital microscopy to identify and measure pitting corrosion. We also utilize computational modeling to predict the progression of pitting under operational conditions, enabling proactive maintenance planning.
summarize :
In summary, our company’s approach to the inspection of metallurgical composite pipes is characterized by a comprehensive understanding of the complex corrosion mechanisms that can affect these structures. By employing state-of-the-art technologies and expert analytical skills, we ensure that SCC, intergranular corrosion, and pitting corrosion are effectively identified and managed. Our commitment to precision, reliability, and continuous improvement in inspection processes sets us apart, guaranteeing that our clients receive metallurgical composite pipes of the highest quality and durability.