S355 MLO steel pipe is a high-strength steel pipe specially designed for Marine engineering with excellent corrosion and wear resistance.
Here are some key takeaways about the S355 MLO Marine structural tube:
1. Material characteristics
- S355 Steel: S355 is a low-alloy high-strength structural steel with good weldability and mechanical properties, suitable for structures that bear large loads.
- Multi-layer coating (MLO) : Through the multi-layer coating process, the pipe surface can increase wear and corrosion resistance and extend the service life.
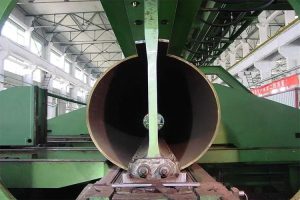
2. Application field
– Marine engineering: Used for offshore platforms, subsea pipelines, wind power infrastructure, etc.
– Oil and Gas: Transport oil and gas in harsh Marine environments for safety and effectiveness.
– Chemical and other industries: used in chemical media and corrosive environments.
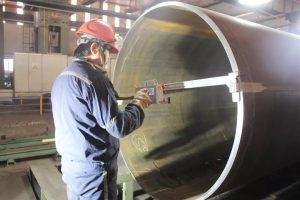
3. Manufacturing process
When welding S355 MLO steel pipes, there are several key factors that need special attention to ensure the quality of the welding and the performance of the final product. Here are some of the main considerations:
①. Material preparation
Clean the surface: ensure that the welding area is free of oil, rust and other impurities to improve the quality of welding.
– Proper cutting: the cutting edge should be flat to avoid irregular shape affecting the welded joint.
②. Welding process selection
– Welding method: The selection of the appropriate welding method (such as MIG, TIG, submerged arc welding, etc.) should be determined according to the material characteristics and application requirements.
– Welding parameters: Adjust parameters such as current, welding speed and gas flow according to material thickness and welding position.
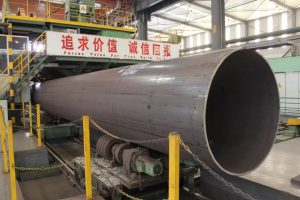
③. Welding sequence
– Layered welding: For multi-layer covering welding, it is recommended to perform the welding layer by layer, ensuring that each layer is cooled to the appropriate temperature before welding the next layer.
– Control deformation: reasonably plan the welding sequence to reduce thermal deformation during welding.
④. Heat input control
– Heat Affected Zone (HAZ) : Control the heat input to avoid material performance degradation due to excessive heat affected zone.
– Preheating and post-heating: Depending on the specific situation, preheating or post-heat treatment may be required to reduce welding stress and improve toughness.
⑤. Welding filler material
Select the right wire: Ensure that the filler material is compatible with the base material to ensure the strength and corrosion resistance of the welded joint.
Multilayer welding: In MLO welding, the selection and application of filling materials should consider their impact on the performance of the overlay.
⑥. Welding post-processing
– Non-destructive testing: After the welding is completed, non-destructive testing (such as ultrasonic, X-ray, etc.) is carried out to ensure the quality of welding.
– Post-heat treatment: If necessary, heat treatment is performed to eliminate welding stress and improve material properties.
⑦. Environmental factors
– Temperature and humidity: The welding environment should be suitable, and welding under extreme temperature or humidity conditions should be avoided to prevent welding defects.
⑧. Personnel training
– Welder qualification: Ensure that the welding operator is professionally trained and has the appropriate welding skills and experience.
⑨. Records and documentation
– Welding record: record all parameters and steps in the welding process to facilitate subsequent quality tracking and review.
By following these precautions, you can improve the welding quality of S355 MLO steel pipes and ensure their reliability and safety in harsh Marine environments.
4. Standards and norms
– Production and inspection should comply with international standards and industry norms, such as API, ISO, EN and other standards, to ensure product quality and safety.
5. Testing and certification
– Perform non-destructive testing (NDT), mechanical performance testing, corrosion resistance testing, etc., to ensure product compliance with design and safety standards.
– Certification may be required to meet the requirements of a specific project or industry.
6. Design considerations
In the design of Marine structural pipelines, corrosion, fatigue, wave load and other factors in the Marine environment should be considered to ensure the safety and reliability of the structure.